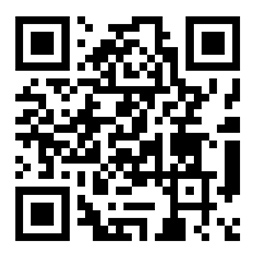
工业金属管道施工及验收
一、洗油工程工艺管线的施工按照GB50235—97《工业金属管道工程施工及验收规范》,及GB50236—98《现场设备、工业管道焊接工程施工及验收规范》进行。
二、本工程工艺管线的施工 严格按照图纸的的所有要求进行。
三、管子、管道附件及阀门的检验
(1) 管子、管道附件(简称管件),阀门 具有制造厂的合格证明书,其指标应符合现行或部颁技术标准。
(2) 在使用前应进行外观检查,要求其表面。
1 无裂纹、缩孔、夹渣、重皮等缺陷。
2 不超过壁厚偏差的锈蚀或凹陷。
3 螺纹密封面良好,精度及光洁度应达到设计要求或制造标准。
4 合金钢应有材质标记。
(3) 合金钢管及其管件在使用前均应用光谱分析或其他方法进行复查,并作标记。
(4) 低压阀门(PN1.6~2.5MPa)应从每批中(同制造厂、同规格、同型号、同时到货)中抽查10%进行强度和严密性试验,若有不合格,再抽查20%,如仍有不合格,则需逐个检查,阀门的试验压力为公称压力的1.5倍(用洁净水试压)。
(5) 用在油品>200℃操作温度的阀门, 进行逐个用煤油进行试验,并须对阀门大盖的原有垫片进行检查,需要用缠绕垫片。对<200℃操作温度的阀门大盖垫片 用耐油石棉垫片。
(6) 对不锈钢阀门应逐个对壳体进行光谱分析,复查材质,每批取10%且不少于1个,进行解体检查内部零件。如有不合格则需逐个检查。
四、管道焊接
(1) 施工单位 有负责焊接工程的焊接技术人员,焊接检查人员,焊接检验人员及 焊工。焊工须经考试合格持证上岗。
(2) 施工单位所用焊接设备 是有参数稳定、调节灵活、满足焊接工艺要求和的性能。
(3) 施工单位 根据检验要求提供检验设备,以检测焊缝质量。
(4) 管子、管件的坡口型式、尺寸,除按设计施工图纸规定进行外,当设计无规定时,一律按上述规范的管道焊接章节的内容进行。
(5) 管子、管件组对其内壁应做到平齐,内壁错边量不能超过壁厚的10%,并应检查坡口的质量,坡口表面上不得有裂纹、夹层等缺陷,对坡口及其内外侧进行清理掉油、漆、锈、毛刺等污物,清理合格后应及时施焊。
(6) 按 管道材质、温度、压力,为参数的分类,按上述规范规定,洗油工程应为Ⅳ类管道。
对应的焊缝等级为Ⅲ级。
(7)管道焊后 对焊缝进行外观检查,各级焊缝表面质量标准见上述规范规定,外观检查应在无损探伤强度试验之前进行。
(8) Ⅲ级焊缝等级的管道焊缝射线探伤数量为固定焊口10%,转动焊口5%。
五、管道安装。
(1) 管道的坡向、坡度、应符合设计要求。
(2) 管道的坡度,可用支座下的金属垫板调正,吊架用吊杆螺栓调正。
(3) 法兰焊缝及其它连接件的设置应便于检修,不得紧贴墙壁、楼板或管架上。
(4) 合金钢管不应焊接临时支撑物,如有 时应符合焊接的有关规定。
(5) 法兰连接时应保持平行,其偏差不大于法兰外径的1.5/1000,且不大于2mm,不得用强紧螺栓的方法歪斜。
(6) 法兰连接应保持同轴,其螺栓孔 偏差一般不超过孔径的5%,并螺栓自由穿入。
(7) 双头螺栓应对称均匀,松紧适度,紧固后,外露长度不大于2倍螺距,两头外露长度应相同。
(8) 与传动设备连接的管道,安装前, 将管道内部处理干净,在管道与传动设备法兰连接前,应在自由状态下,检查法兰的平行度和同轴度,允许偏差见下表:
设备转速(转/分) 平行度(mm) 同轴度(mm)
3000 ≤0.15 ≤0.50
(9) 管子对口时应检查平直度,允许偏差1mm/m,但全长允许偏差大不超过10mm,管道连接时,不得用对口加热管子等方法来接口端面的空隙、偏差、错口或不同心等缺陷。
(10) 管道预拉伸, 符合设计规定。
(11) 管道焊缝位置应符合下列要求:
1 直管段两环缝间距不小于100mm
2 环焊缝距支、吊架净距不小于50mm
3 在管道焊缝上不得开孔。
4 管道上仪表接点的开孔和焊缝应在管道安装前进行。
(12) 穿墙及过楼板的管道,一般应加套管,但管道焊缝不得置于套管内。
(13) 不锈钢管道安装时,不得用铁质工具敲打。
(14) 不锈钢管道与支架之间应垫入不锈钢、不含氯离子的塑料或橡胶垫片,防止不锈钢管与碳素钢直接接触。
(15) 管道安装允许偏差如下:
项目 允许偏差(mm)
1 坐标及标高 室外架空、
室外地沟、
室内架空、
室内地沟, 15
15
10
15
2 水平管弯曲 DN≤100
DN>100 1/1000 (大20)
1.5/1000 (大20)
3 立管垂直度 2/1000 (大5)
4 成排管段 在同一平面上
间距 5
+5
(16) 蒸汽伴热管应与主管平行安装,位置、间距正确,水平伴管一般应安装在主管下方或靠近支架的侧面,伴管可用绑扎带或镀锌铁丝等固定在主管上,其绑扎点间距为:
伴管DNmm 绑扎点间距m
10 0.8
15 1.0
20 1.5
>20 2.0
(17) 对不允许与主管直接接触的伴管,在伴管与主管间应有隔离垫。
(18) DN≤50mm的碳素钢管,一般应用机械法切割。不锈钢管(316L)应用等离子方法或机械法切割。
(19) 预制完毕的管段,应将内部清理干净,封闭管口,不得有杂物进入。
六、夹套管的制作安装
(1) 参照FJJ211—86《夹套管施工及验收规范》进行。
(2) 夹套管的施工应符合设计文件的规定。
(3) 根据夹套管的分类,本工程的夹套管内管的工作温度为<350℃,设计压力0~16kg/cm2,分类为Ⅲ类低压管道,外管工作温度<350℃,设计压力为0~16kg/cm2,分类为Ⅱ类低压管道。
(4) 夹套管的预制工作应在清洁、避风、环境温度>0℃的预制 车间进行。
(5) 为了夹套管的焊接质量,氩弧焊室外作业环境风力等级不宜超过2级,否则,需加防风措施。
(6) 内管。外管的内腔 清扫洁净,管道若有明显的油迹, 进行脱脂处理。
(7) 管子端面垂直度偏差值不得大于下表的规定值:
管子DN 25—70 80—100 125—150
偏差值(mm) 0.5 0.7 0.9
(8) 管子的切口、坡口,应用机械方法进行,不宜用手工火焰切割。
(9) 为了内外管的夹套间隙,满足工艺要求,应按设计要求制作安装定位板,定位板与外管内壁间隙以1.5mm为宜。
(10) 夹套管内、外管同心度偏差值应符合下表规定。
内管公称直径 内外管同心度偏差值
DN≦150 <1.5mm
(11) 夹套管预制件的焊缝抽检10%进行射线探伤,如其中有不合格者,按原规定比例加倍探伤,如仍有不合格者,应对该管的全部焊缝进行射线探伤。
(12) 套夹管安装的坐标、标高、水平度、垂直度应符合设计要求其偏差值不应超过下列规定。
坐标偏差 ±10mm
标高偏差 ±5mm
水平度偏差 ≦1/1000 大不超过20mm
垂直度偏差 ≦1/1000 大不超过15mm
(13) 夹套管安装时,不应使其重量作用于转动设备上,不得强制对口。
(14) 夹套管法兰在紧固前应检查其结合面的不平行度和间隙偏差。紧固后应检查法兰 线的偏移值,其误差不应超过下面的规定。
法兰允许偏差值(mm)
法兰连接位置 不平行度 间隙 偏移
一般转动设备 ≦ 0.15 ≦ 0.5 ≦ 0.5
高速转动设备 ≦ 0.1 ≦ 0.3 ≦ 0.2
一般容器 ≦ 0.5 ≦ 1.0 ≦ 1.0
一般配管 ≦ 0.5 1~1.5 ≦ 1.0
(15) 安装夹套管的外管连通管应防止存液,并应焊在夹套的两端,水平连通管应由夹套管底部沿切线方向引出。
(16) 夹套管内的主管不应有焊缝。
七、.阀门安装
(1) 阀门安装前应检查填料,其压盖螺栓须有足够的调节余量。
(2) 安装阀门前,应按设计图纸核对型号,并按介质流向确定其安装方向。
(3) 法兰或螺纹连接的阀门应在关闭状态下安装。
(4) 对焊阀门与管道连接焊缝底层宜采用氩弧焊施焊以内部清洁。焊接时阀门不宜关闭,防止过热变形。
八、安装“∏”形或“Ω”形补偿器,应按设计规定进行预拉伸,允许偏差±10mm水平安装时,平行臂应与管线坡度相同,垂直臂应呈水平,垂直安装时,应有排气及疏水装置。
九、支、吊架安装
(1) 管道安装时,应及时进行支、吊架的固定和调正工作,支、吊架位置应正确,安装平正牢固,与管子接触良好。
(2) 固定支架应严格按设计要求安装,并在补偿器预拉伸前固定。
(3) 导向支架或滑动支架的滑动面应洁净平整,不得有歪斜和卡涩现象。
(4) 弹簧支、吊架的弹簧安装高度,应按设计要求调整。
十、工程交工验收时,施工单位应提交下列技术文件:
(1) 施工单位和建设单位共同检查、并进行签证的资料。
A管道的预拉伸资料。
B管道系统强度、严密性试验等资料。(液体强度实验压力为设计压力的1.25倍)
C管道系统吹洗资料。
D隐蔽工程等资料。
(2) 施工图、设计修改文件及材料代用记录。
(3) 焊接表面质量检查报告。
(4) 焊缝无损探伤报告(焊缝内部质量检查报告)。
(5) 焊缝返修后质量报告。
(6) 竣工图:工程变不大时,由施工单位在原施工图上加以注明即可